The secret to successfully cutting metal with water is to keep the spray consistent. Waterjets cut because an extremely small-jeweled nozzle directs the spray at high pressure, allowing the spray to remain coherent. Unlike metal cutters, a waterjet never dulls and cannot overheat.
A waterjet cuts through a “sandwich” of diverse materials with a thickness of up to four inches. This dust-free, odorless, and virtually heat-free method may also cut through materials as thin as 5,000ths of an inch. Because of the modest jet stream, the first cut can also be the ultimately finished surface. A CNC waterjet machine saves money on both material and machining costs through the single-cutting procedure.
Techni Waterjet discusses what waterjet cutting can do in metalworking.
Fundamentals
Pure vs. Abrasive
In its broadest definition, the phrase “waterjet” refers to any cutting instrument that makes use of a high-pressure stream of water. Waterjets further subdivide into pure and abrasive divisions.
Pure waterjets are the original form of the technology and function just as their name suggests, cutting with a spray of pressurized water. They are suitable for softer materials such as gaskets, paper, plastic, and carpet. However, the benefits of pure ones are limited to cutting soft and/or thin materials such as foam, fabric, cardboard, foil, rubber, and wood.
Abrasive waterjet technology extends the benefits of pure waterjet technology to cutting tougher materials such as metal, wood, glass, ceramic, and stone. Abrasive ones are primarily constructed of garnet and range in grit size from 50 to 220 mesh, with 80 being the most prevalent.
Many machines can switch between pure cutting and abrasive cutting. Thus, this makes them highly versatile.
Cutting Metals with a Waterjet
Abrasive waterjets are perfect for challenging and profitable metal cutting applications. Abrasive ones may cut titanium, Inconel®, brass, and tool steel besides conventional materials like mild steel and aluminum. Whether you are cutting 8-inch-thick titanium or 1/4-inch-thick aluminum, flow waterjets are versatile enough to cut a wide range of shapes and materials.
The Most Effective Edge
Secondary processing is usually avoidable, because there is no mechanical stress, heat distortion, or heat-affected zone (HAZ). Straight from the waterjet table, you can get a satin-smooth edge.
Kerfs to a Minimum
Because waterjets are cut with a narrow kerf, typically 0.030″ to 0.040″, parts can be densely nested or common-line cut. This maximizes raw material use. Kerf in waterjet cutting results in less waste on your floor and more money in your pocket.
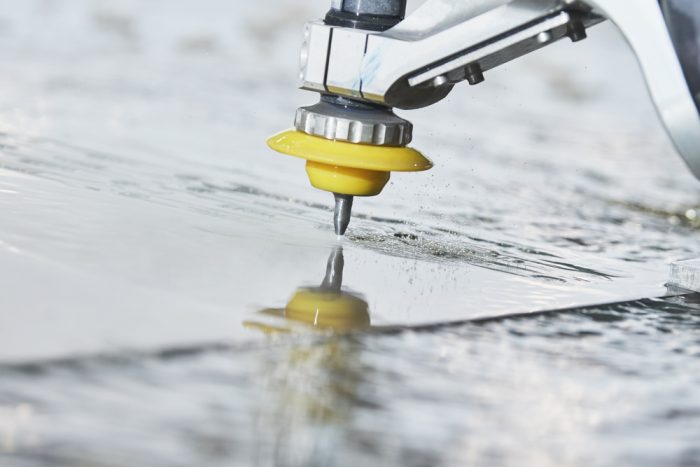
Key Advantages of Cutting Metals with a Waterjet
- Productivity gains, rapid cutting, and high-quality parts
- Incredible detail is possible with a small kerf.
- Inconsistent material is not an issue (there is no need for costly ‘laser ready’ material).
- Savings on raw materials — less scrap
- There is no need for substantial part clamping, and lateral or vertical stresses are kept to a minimum.
- Depending on the material thickness, single-pass cutting
- There is no heat damage.
- Cutting net or near-net, with little or no hand finishing
Can Water Cut Through Steel?
Water cutting through rigid surfaces may seem impossible to imagine. After all, it is water, and we are discussing hard materials such as steel —not softer materials such as paper or foam.
Water dynamics change considerably when the speed and high-pressure stream of water is raised sufficiently. Water becomes a destructive force capable of cutting steel and other hard materials more effectively than mechanical cutting instruments.
You might be astonished at how well this machine cuts through the steel and how few constraints it has. We will go through some of these constraints later. For the time being, let us look at how a waterjet cuts through steel.
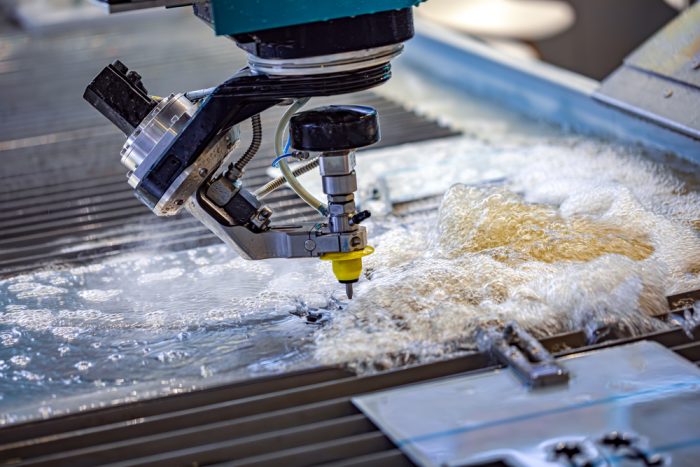
What Is the Process of Cutting Metal with One?
Have you ever observed how high-pressure water at a car wash makes your car look brand new in minutes? The pressure we are discussing here is 1,000 psi. Doesn’t that seem like a lot of pressure?
When we talk about high-pressure waterjet cutting, we’re referring to water pressures ranging from 50,000 to 60,000 psi. Consider what this high-pressure water can accomplish! It can easily cut through steel and a variety of other materials. A high-pressure pump, specialized high-pressure tubing, and a narrow nozzle, or cutting head, produce a powerful yet tiny jet stream.
Water Cuts Steel at What Pressure?
The needed water pressure varies depending on the type of abrasive material, abrasive thickness, and steel type. Water pressure typically ranges between 20,000 and 55,000 psi. Abrasives that are smaller, harder, and more consistent require less water pressure.
How Many Inches of Steel Can They Cut?
Theoretically, the thickness of steel that sophisticated waterjets can cut is limitless. However, when cutting a thick piece of steel, the time required increases dramatically, rendering the procedure impractical.
As a result, waterjet cutting equipment can often cut up to 6 inches of steel. However, commercially available equipment can handle up to 9 inches.
Advanced abrasive and percussive waterjets adjust in some applications to cut 18-inch thick steel blocks. However, such thickness is not routinely employed.

What Are the Advantages of This Cutting Process in Metalworking?
Now that you know cutting metal with abrasive waterjets is possible, the question is whether the technique is beneficial. Waterjet cutting has many advantages that make it more effective and preferred over other cutting methods.
No Heat-Affected Zone (HAZ)
Unlike other metal cutters, waterjet cutting is a heat-free operation. Hence, no heat-affected zone is formed when cutting metal. Heat-affected zones can compromise the material’s integrity, potentially weakening it near the cut location. Because these zones are removed in waterjet cutting, the material cannot overheat, preserving its integrity.
Excellent Finishing
There is no discoloration, and the cut is cleaner since there is no heat-affected zone in the workpiece. This results in a better finish right off the table. It also avoids the need for any extra finishing, as opposed to metal cutters, which leave the final completed surface unfinished.
High Cut Quality
Even on small kerf cuts, the cutting stream from abrasive waterjets flows consistently through the material. As a result, the cut quality is precise. Running your touch over the chopped material will reveal a clean edge.
Designs and Shapes
Waterjet cutting provides many change options, and abrasive ones can be controlled with CNC. Because they are not limited to straight lines, they cut a wide range of forms and designs. Hence, they are perfect for manufacturing complex components.
Efficiency
Multiple layers of material can be stacked on top of each other and cut together with a waterjet cutter. This improves the overall efficiency of the cutting operation.
Tolerances for Precise Cutting
Tolerance refers to the variation from the desired cut. As a result, it is inversely related to accuracy. Waterjet cutting is one of the most exact processes, resulting in consistently, properly cut metal products.
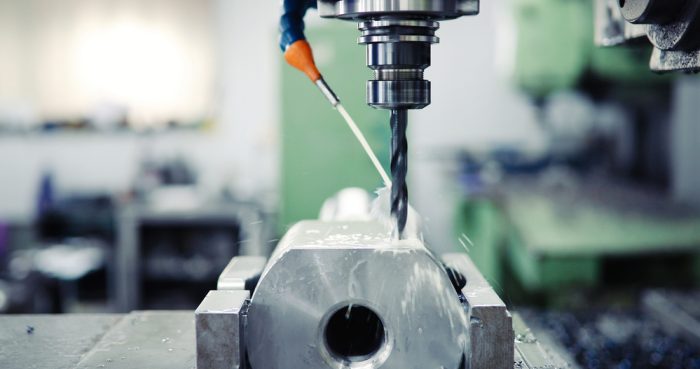
What Are Common Applications for Waterjet Cut Metals?
As you can see from the preceding section, waterjet cutting offers many advantages over other cutting technologies. As a result, waterjet cut metal parts are in high demand for a wide range of applications. Here are a few examples of such applications:
Components of an Engine
5 or 6-axis waterjet cutters produce sophisticated structures such as complex engine parts since waterjet cutting is a multi-axis cutting process. Abrasive waterjet cutting makes many of the microscopic parts seen in today’s automobile sector. Its precision helps to reduce machining expenses.
Processing of Raw Materials
All metalworking industries utilize steel as a raw material. It is frequently chopped into small sheets and blocks before transit and storage. Waterjet cutting accomplishes this.
Architecture and Art
Waterjets cut workpieces and punch holes in the material to create various artwork designs. Interior design and architectural projects employ these designs.
Medical Instruments
Waterjet cutting is a precise process that does not require the cutting tip to contact the object to be cut. This makes it perfect for cutting surgical tools and surgical equipment.
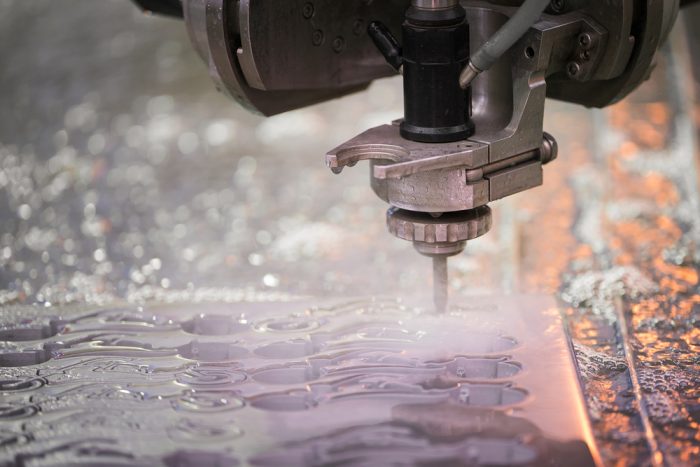
Final Words
Cutting steel using a high-pressure water stream is one of the greatest ways to produce excellent results while saving money on material and machining. There is no risk of material deterioration or particles flying around.
The ultimate result is smooth and clean cuts that do not require additional finishing operations. After the cutting procedure, use the steel parts as is.
When it comes to cutting alternatives for steel items, waterjet cutting is the greatest option. Even if you purchase one to cut steel, you can use it to cut other materials as well. It is also perfect for cutting materials such as wood, stone, tempered glass (even bulletproof glass) and other materials.
Find a Home-Based Business to Start-Up >>> Hundreds of Business Listings.