In today’s competitive market, the race to develop products that cater to consumer demands and stand out in quality and design is more intense than ever. With many manufacturing techniques available, selecting the optimal method can be a game-changer for businesses.
Among these various techniques, one has notably gained prominence, offering a combination of precision, scalability, and adaptability: custom injection molding. This process, prevalent in many industries, sets new benchmarks in product development.
But what makes custom injection molding such a sought-after method? And how can it redefine the trajectory of product creation? Continue reading to discover the transformative role of custom injection molding in product development and why it’s becoming a favorite for manufacturers globally.
The Basics of Custom Injection Molding
The manufacturing sector continually evolves, striving for efficient and innovative techniques. To get a clearer picture of its significance, here are the foundational aspects of this technique:
- Process dynamics: At its core, custom injection molding involves injecting molten materials, primarily plastics, into molds. This process ensures that every product is uniformly shaped and retains intricate details.
- Mass production efficiency: Custom injection molding’s true strength lies in its scalability. Once you set up the mold, it enables the production of large quantities without sacrificing quality, making it ideal for large-scale manufacturing projects.
- Design intricacy: This method is renowned for its ability to reproduce intricate designs with impeccable accuracy. Whether it’s the delicate curves of a product or the fine lines of a prototype, custom injection molding captures it all.
Breaking down the fundamentals of custom injection molding reveals that its foundational elements aim to optimize product development. From design fidelity to efficient mass production, it embodies the essence of modern manufacturing.
Why It Matters in Product Development
Product development is a multifaceted process, with every step demanding attention to detail and efficiency. Amidst various manufacturing methodologies, why does custom injection molding hold significant importance?
Below are compelling reasons that highlight its value:
- Precision-driven outcomes: Accuracy is paramount in product development. Custom injection molding guarantees products that adhere closely to design specifications, ensuring every detail is on point.
- Cost efficiency: Custom injection molding offers long-term benefits like waste reduction, fewer defects, and high-volume production, which outweigh its initial setup costs, making it cost-effective for manufacturers.
- Speed to market: Quick product delivery is crucial in today’s fast-paced market. This method allows for rapid prototype development and iterations, drastically reducing lead times.
- Adaptability: Custom injection molding offers flexibility for design changes, material experimentation, and responding to market feedback, enabling manufacturers to adapt quickly.
- End-product integrity: Beyond aesthetics, custom injection molding produces items that are durable, functional, and reliable, ensuring users get the quality they expect.
At its core, custom injection molding equips product developers with a tool that simplifies manufacturing and elevates their offerings’ quality and market readiness.
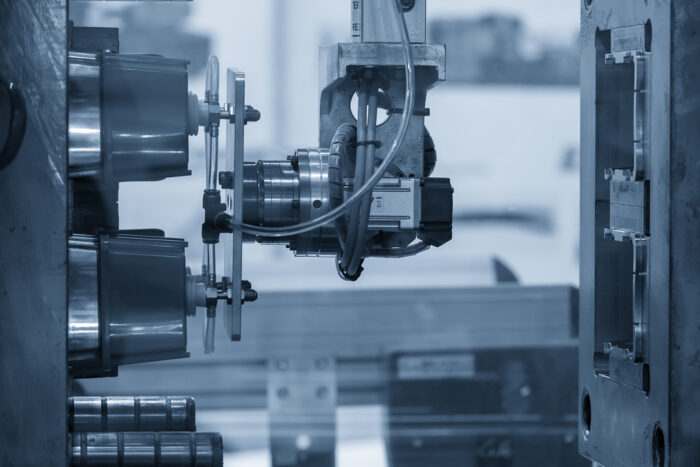
Incorporating Sustainability
As the global push for eco-friendly practices intensifies, manufacturers seek methods aligning with these values. Custom injection molding, with its inherent attributes, emerges as a frontrunner.
Here are some ways it champions sustainability:
- Resource efficiency: Custom injection molding minimizes material wastage. Excess material can be recycled and reused, leading to optimized use of resources and reduced scrap.
- Energy consumption: Advanced machinery used in this method often operates on lower energy, contributing to reduced carbon footprints and lesser energy expenditure.
- Reduced emissions: With a streamlined process and modern machinery, custom injection molding can produce fewer greenhouse gas emissions, fostering a cleaner production environment.
- Durable products: Products made through custom injection molding have a longer life span, reducing the frequency of replacements and less burden on waste management systems.
- Material options: Many eco-friendly and biodegradable materials are compatible with custom injection molding, allowing manufacturers to create greener products.
Indeed, embracing custom injection molding is a step towards a sustainable manufacturing future. It’s pivotal in shaping an eco-conscious product development landscape by minimizing waste, conserving energy, and offering durable solutions.
How to Implement This Method
Integrating custom injection molding into your manufacturing process might seem complex, but it becomes a seamless transition with careful planning and understanding.
If you’re considering this approach, the following steps will guide you:
- Research and planning: Begin with a comprehensive understanding of the product you aim to produce. What materials are best suited? What design intricacies are needed? This foundational knowledge will shape your molding strategy.
- Select the right machinery: Invest in high-quality injection molding machines. While numerous options are available, choosing machinery tailored to your product’s specifics and desired output is essential.
- Prototype development: Before going full-scale, creating prototypes will help identify design flaws, material inconsistencies, and other potential issues, allowing for refinement.
- Partner with experts: If you’re new to custom injection molding, consider collaborating with experienced professionals or consultants. Their insights can be pivotal in growing a successful business and avoiding common pitfalls.
- Continuous monitoring: Even after implementation, monitoring the production process ensures consistent quality, efficient operations, and timely identification of any areas needing adjustment.
Adopting custom injection molding into your product development cycle amplifies efficiency and quality. With careful planning and a keen eye for detail, you’ll harness its full potential, ensuring top-tier results with every production run.
Conclusion
Product development demands precision, efficiency, and innovation in today’s competitive market. Custom injection molding offers a blend of these qualities, streamlining manufacturing while upholding product integrity. By understanding its nuances and integrating its principles, manufacturers position themselves at the forefront of excellence, delivering products that resonate with modern demands and stand the test of time.
Find a Home-Based Business to Start-Up >>> Hundreds of Business Listings.