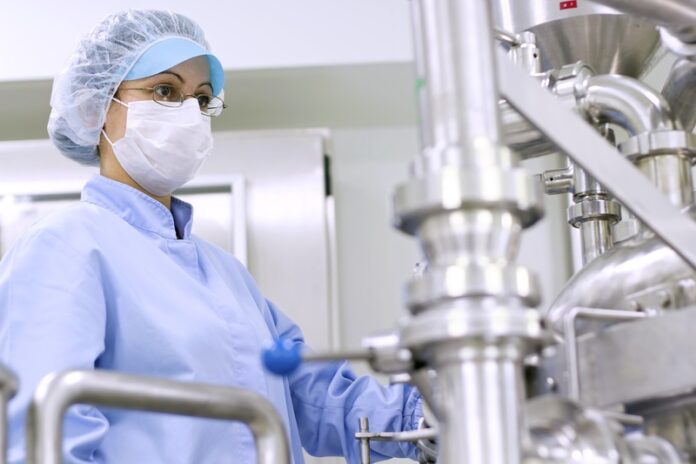
Are you curious about how chemical manufacturing is evolving?
Wondering what innovations are shaping this essential industry and how these changes might impact various sectors?
The chemical manufacturing industry is a cornerstone of modern development.
With the constant push for sustainable and efficient processes, recent innovations are reshaping the landscape, offering significant improvements and opportunities for advancement.
Understanding these transformations can provide valuable insights into the future of manufacturing and its broader implications.
Digitalization and Automation
The integration of digital technologies is revolutionizing chemical manufacturing, making it more efficient, safe, and responsive to market needs.
The Rise of Automation
Automation in modern chemical manufacturing is not just about replacing human labor with machines.
It involves using advanced robotics and artificial intelligence to optimize production processes.
By automating repetitive tasks and monitoring complex systems, companies can increase efficiency, reduce errors, and minimize operational costs.
For example, automated systems can precisely mix chemicals and monitor reaction conditions, ensuring consistent quality and safety standards.
Digital Twins
Digital twins are virtual replicas of physical assets, processes, or systems.
They provide a dynamic, real-time simulation environment for testing changes and predicting outcomes before implementing them in the real world.
In chemical manufacturing, digital twins can model production facilities, allowing operators to simulate changes in process conditions, optimize performance, and anticipate maintenance needs.
This innovation reduces downtime, improves safety, and enhances overall efficiency.
Sustainable Manufacturing Practices
With growing environmental concerns, the chemical manufacturing industry is under pressure to adopt sustainable practices.
Green Chemistry
Green chemistry involves designing products and processes that minimize the use and generation of hazardous substances.
This approach reduces waste, conserves resources, and lowers the environmental impact of chemical manufacturing.
More companies are adopting green chemistry principles to develop eco-friendly products and processes.
For instance, they are using renewable feedstocks, designing biodegradable products, and employing safer reaction conditions.
Energy Efficiency
Reducing energy consumption is crucial for sustainable manufacturing.
Innovations in process design and energy recovery systems are enabling more energy-efficient chemical manufacturing operations.
Heat integration, advanced catalysts, and renewable energy sources are some of the strategies being implemented to achieve this goal.
By improving energy efficiency, manufacturers can reduce emissions and decrease operational costs.
Biotechnology Integration
The integration of biotechnology into chemical manufacturing offers exciting new possibilities.
Enzyme Catalysis
Enzymes, nature’s catalysts, are now being used in chemical manufacturing to drive reactions under milder conditions compared to traditional chemical catalysts.
This approach not only reduces energy requirements but also minimizes by-products and waste.
Enzyme catalysis is particularly beneficial in producing pharmaceuticals, fine chemicals, and biofuels.
Biopolymers
Biopolymers are polymers derived from living organisms, and they represent a sustainable alternative to conventional petrochemical-based polymers.
They are biodegradable, reducing the environmental impact associated with plastic waste.
In chemical manufacturing, the use of biopolymers is gaining traction, especially in packaging, textiles, and agricultural applications.
Advanced Materials and Nanotechnology
Advancements in materials science and nanotechnology are opening new avenues for innovation in chemical manufacturing.
Nanomaterials
Nanomaterials exhibit unique properties at the nanoscale, making them suitable for various applications.
In chemical manufacturing, they are used to enhance the performance of catalysts, coatings, and composite materials.
Nanomaterials enable more efficient chemical reactions, improve product quality, and reduce material consumption.
For instance, nano-catalysts can increase reaction rates and selectivity, leading to more efficient processes.
Smart Materials
Smart materials respond dynamically to external stimuli, such as temperature, pH, or light.
These materials find applications in self-healing coatings, responsive drug delivery systems, and sensor technologies.
The development and integration of smart materials in chemical manufacturing can improve product functionality and enable new applications.
Circular Economy Adoption
The concept of a circular economy is gaining traction in the chemical manufacturing industry.
This approach emphasizes reusing materials, minimizing waste, and maintaining the value of products and materials for as long as possible.
Waste Valorization
Waste valorization involves converting waste materials into valuable products.
In chemical manufacturing, waste streams can be turned into feedstocks for other processes or transformed into energy.
This reduces the environmental footprint and creates economic value
Technologies like pyrolysis, gasification, and fermentation are employed to achieve waste valorization.
Chemical Recycling
Chemical recycling breaks down plastic waste into its chemical building blocks, which can be used to synthesize new materials.
Unlike mechanical recycling, which degrades material quality, chemical recycling allows for the recovery of high-quality feedstocks suitable for producing new plastics.
This innovation supports the development of a circular economy and reduces reliance on virgin raw materials.
Conclusion
The chemical manufacturing industry is undergoing a profound transformation driven by technological innovations and sustainable practices.
The integration of digital technologies, adoption of green chemistry, biotechnology advancements, novel materials, and circular economy principles are reshaping the future of chemical manufacturing.
This industry plays a vital role in numerous sectors, and its continued evolution promises to deliver improved efficiency, reduced environmental impact, and new opportunities for growth.
Stay informed about these trends to leverage the potential of chemical manufacturing innovations in your network.
By harnessing these advancements, businesses can stay competitive, meet regulatory demands, and contribute positively to global sustainability goals.
Find a Home-Based Business to Start-Up >>> Hundreds of Business Listings.